Mühlböck progressive kiln DYNAMIC
The wood is exposed to different climatic conditions depending on the drying requirement. Depending on the type of wood, wood dimension, initial moisture content, desired final moisture content and quality requirements, the Mühlböck progressive kiln is designed with different climate zones.
A fully automatic and optimized feeding system ensures trouble-free transport of the wood through the kiln. The new security system also ensures smooth operation during operation.
Depending on customer requirements, the drying systems can be individually designed and built.
Mühlböck progressive kiln DYNAMIC
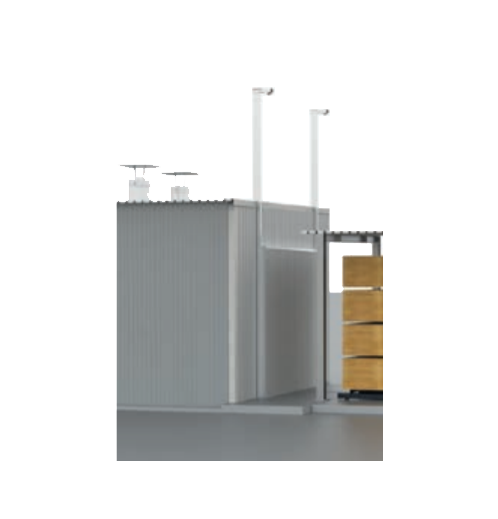
PROGRESSIVE KILN DYNAMIC PLUS
2-zone progressive kiln
The progressive kiln DYNAMIC Plus can be used for drying in any area of wood production. This version of the plant is suitable for customers for whom thermal energy consumption plays a minor role. Due to excellent drying conditions with this progressive kiln, the best possible timber quality with reduced shrinkage is guaranteed.
The drying plant is designed as a 2-zone progressive kiln with main- and final drying zones.

PROGRESSIVE KILN DYNAMIC 1306 PRO
2-zone progressive kiln with heat recovery system 1306 PRO
The progressive kiln DYNAMIC 1306 PRO can be used in all areas of wood production for drying.
An essential feature of this system is that with optimized throughput due to the use of heat recovery, the thermal energy consumption can be reduced by up to 25%. Thus, the progressive kiln DYNAMIC 1306 PRO represents an optimal solution in the combination of thermal and electrical energy consumption, drying capacity, and investment costs of the system.
The drying plant is designed as a 2-zone progressive kiln with main and after-drying zones. The division of the zones can be individually tailored to the wishes of the customer.

PROGRESSIVE KILN DYNAMIC 1003 PREMIUM
3-zone progressive kiln with heat recovery system 1003 PREMIUM
Three drying zones are implemented in the 1003 PREMIUM version; a pre drying zone, a main drying zone and a final drying zone. The total amount of energy input to the heater battery is transferred using heat exchangers from the main and final drying zones to the pre drying zone. No additional energy is required from the heating system for drying in this zone. This enables energy-efficient operation of the plant.
Compared to conventional drying systems (dependent on the application), energy savings of up to 50% can be achieved. Due to the low value of the thermal connection and energy requirement, an increase in the drying capacity is possible, without any further investment in a heat generator, even in the case of energy bottlenecks.